If you overbid, you risk losing out to a cheaper competitor.
But if you underbid, you could be shooting yourself (and your budget) in the foot later down the line. That's where construction job costing comes in.
This is the key challenge that construction businesses face when job costing for new work.
And sure, getting it right can be complicated and time-consuming - but skipping it simply isn't an option if you want to keep your project costs on track and your business in the black.
Here's everything you need to know to get construction job costing right, including:
- What is construction job costing?
- Step-by-step: How to produce a job cost
- Best practices for effective job costing
The basics: Where to start with job costs
Construction job costing is an essential task for companies of all shapes and sizes – and getting it right is key to keeping your projects on budget and your profit margins intact.
There's a lot resting on your ability to produce an accurate number at the start of the project.
Construction job costing is the process companies go through to calculate these numbers up front. This generally involves an outline of the following:
- Labour
- Materials
- Equipment
- Overheads
- Profit margin
By going through each of these areas in detail, it's possible to generate a much more accurate picture of what the job costs will be.
Here's why that's important:
Reduce profit fade:
Keeping your projects on time and within budget means there's less danger of any extra costs eating into your profit margin later in the project.
Optimise costs:
By tracking your expenses and producing accurate job cost reports throughout the project, you can proactively identify ways to reduce costs. This creates lower bills for your customer and/or higher profits for you.
Stop problems in their tracks:
Without a detailed outline and ongoing tracking of your costs, you're essentially flying blind. Construction job costing helps you spot issues before they become problems.
Step by step: How to produce a job cost
It might seem like job costing is simply about producing an accurate estimate at the start of the project. And that's certainly a big part of it.
But really effective job costing doesn't just finish once the quote is sent – it needs to be proactively monitored, managed and optimised throughout the length of the project.
To do this, it's important to break down the estimate in as much detail as possible - and track your actual costs later when they're spent.
This will give you the crucial evidence you need to produce more accurate estimates next time around.
After all, producing a job cost for a two-bedroom house is going to be much easier if you have a blow-by-blow rundown of your costs on the last similar project.
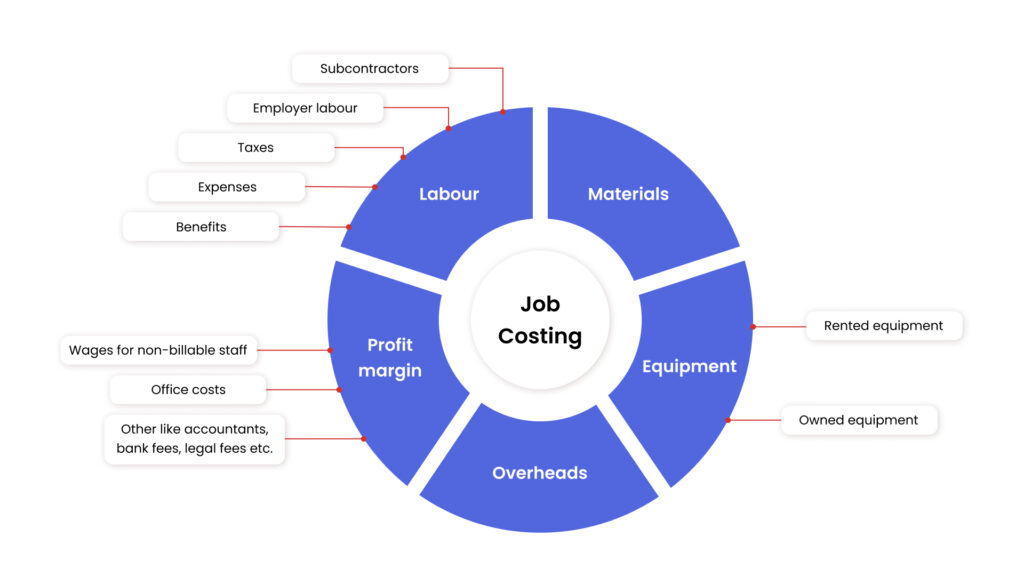
Here's a rundown of everything you need to remember for each section of your job costing:
Labour
The first key thing to bear in mind here is the costs of those who'll actually be doing the work. This should include:
- Subcontractors
- Employer labour
- Taxes
- Expenses
- Benefits
By far the best way to understand your labour needs is to track the time of the workers on the projects. The more granular and detailed that tracking, the more accurate your forecasting is going to be.
The key challenge here is that workers and subcontractors will often work at varying rates and have different expense requirements.
For that reason, it's usually advisable to track and calculate each individual labour expense separately and add them together in the job costing outline.
This makes it easier to produce an accurate estimate, as some of these actual costs will invariably change from job to job – and should be adjusted to accommodate.
Materials
Materials should also be a key consideration of your construction job costing, including wood, concrete, steel, any fittings and really anything else you need to complete the actual project.
In a time of inflation and unreliable supply chains, material costs are less predictable than in previous years – so it's particularly important to get this one right.
Again, the key here is to drill your costs down per material, rather than coming up with a blanket estimate for everything.
That means it'll be easy to adjust later as material costs and needs change.
One mistake that companies often make is not including committed costs in their estimates.
These include any existing contractual agreements for materials that haven't been invoiced. It's important to assign some or all these costs to specific projects so they don't accidentally create a profit fade.
It's also important to add a buffer in case material costs rise mid-project and to cover any unplanned costs. A buffer of 10-15% is common across construction projects.
Equipment
Equipment costs should include anything like drills, safety equipment, diggers etc. The key challenge here when job costing is to distinguish between equipment you own outright vs. that which you own or rent:
- For Rented equipment, it's simply a case of adding the whole price of the rental to the job cost.
- Owned equipment is generally a bit more difficult, as there are no upfront costs for you – but you do need to account for cost-to-run, upkeep, maintenance and depreciating value.
The easiest way to do this is to charge a standing charge for owned equipment, based on the amount you'd expect to rent it for.
As with other costs, it's important to calculate and bill individual material costs separately. You should also carefully track each invoice and cost as the projects run, so you can use them to inform future estimates.
It's also important to regularly assess your equipment inventory vs. market rates for purchase or renting, so you can choose the best option for each project and identify opportunities for further cost savings later down the line.
Overheads
Overhead costs include any expenses that aren't directly associated with a particular project:
- Wages for non-billable staff
- Office costs such as rent, internet, bills
- Other company expenses like accountants, bank fees, legal fees etc.
Essentially, these are the day-to-day costs of running a construction business. Because these aren't project-specific, they can be difficult to accurately cost.
The best way to account for this is to add a flat percentage fee to each project – essentially splitting the cost across all your paying clients.
Profit margin
It's also important to include your profit margin. After all, there's not much point in accepting the project without one. This can differ wildly from client to client, so it's important to reassess this each time you create a new job cost to ensure a good deal for both you and the customer.
Best practices for effective construction job costing
Here are a few handy tips to help you get construction job costing right the first time.
Record in real-time
It's helpful to track labour costs, materials and equipment in real-time, rather than leaving a pile of receipts or timesheets to go through at the end of the month. This helps keep your manual workload down and avoids you working from outdated information.
Report regularly
The more regularly you report, the more quickly you are likely to spot any issues before they start to threaten your budget and profits.
Don't forget overheads and profit margins
These are easy to forget because they're more difficult to assign to specific projects. But they're a vital part of running your business – so make sure not to forget.
Remember change orders
Change orders can ruin the best-planned projects. Make sure you have a clear process for change orders laid out at the start of the project, so the client is clear about what's doable within scope – and what would require extra resources.
Review costs regularly
Labour, maintenance, and equipment costs can change sharply – particularly at the moment. Make sure to review them regularly to avoid getting on the wrong side of price rises.
Get the right tech
Sure, Excel might work for simple projects. But as soon as you start measuring different materials or recording each worker's timesheets, you quickly find it starts to spiral out of control. Luckily, tools like Archdesk can help.
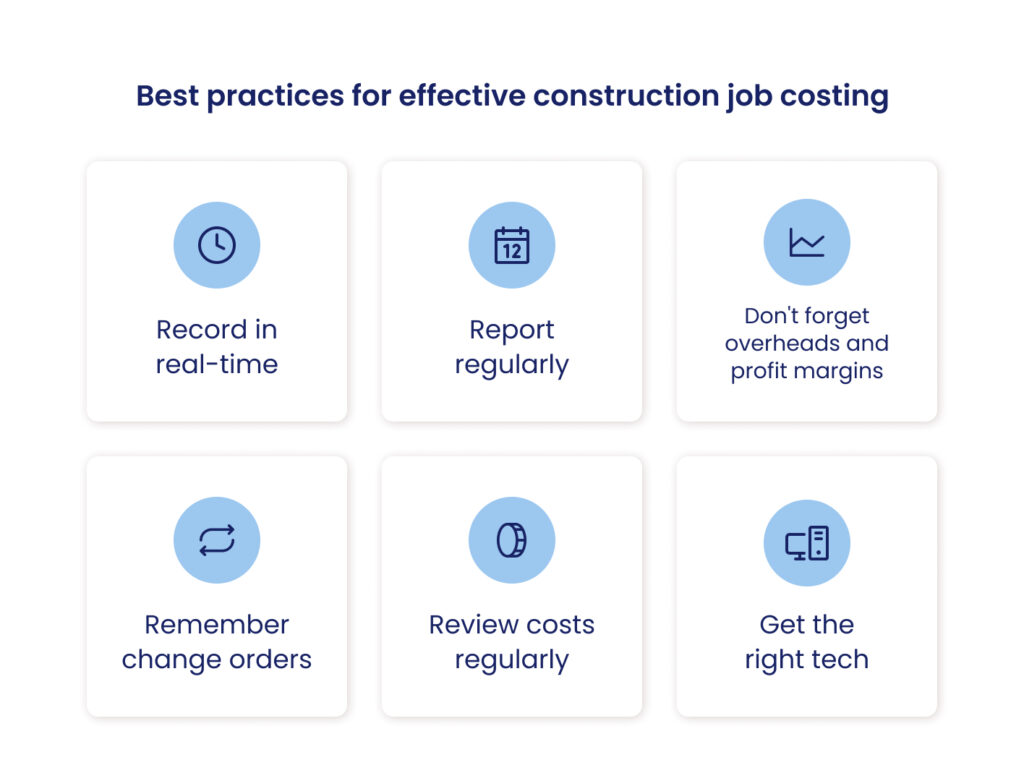
A foundation for job costing success
On the surface, effective job costing sounds like a minefield. And done wrong, it certainly can be. But with the right tools, it doesn't have to be.
Archdesk has job costing functions that make the process easy. Here are just a few examples of that in action:
- Allow workers to complete timesheets on the day, and have your systems updated in real-time. This gives you accurate data of hours worked down to the day – always.
- Keep track of project value, associated costs, and sent/received invoicing with budget control.
- Get a clear view over who's working what job and when with resource scheduling.
- Access specialist tools to help generate and track your sales quotes.
In short, Archdesk gives you all the information you need, available in one clear location so you can estimate, report and improve:
"Archdesk enables our partners to view all this information via companywide dashboards, which in turn allows them to more accurately predict cash flow and take immediate action to limit any potential losses."
Joe Hutahaean, Technical Sales Consultant at Archdesk.
Get in touch today to find out more about what Archdesk can do for you.
Frequently Asked Questions (FAQs) about job costing
How do you calculate job costing?
To calculate your construction job costing, add together your expenses for labour, materials, equipment, and overhead costs as well as your profit margin. Then record every hour worked and expense charged to better inform future cost estimates.
What is costing of construction works?
Also known as construction job costing, this is how building firms calculate the value of a contract. It should include labour, materials, equipment, overhead costs, and profit.
What are the best practices for construction job costing?
For effective job costing, remember to record every expense, report regularly, don't forget overheads and profit margins, review costs regularly, and make sure you have the right technology for the job.